Constant questioning drives improvement
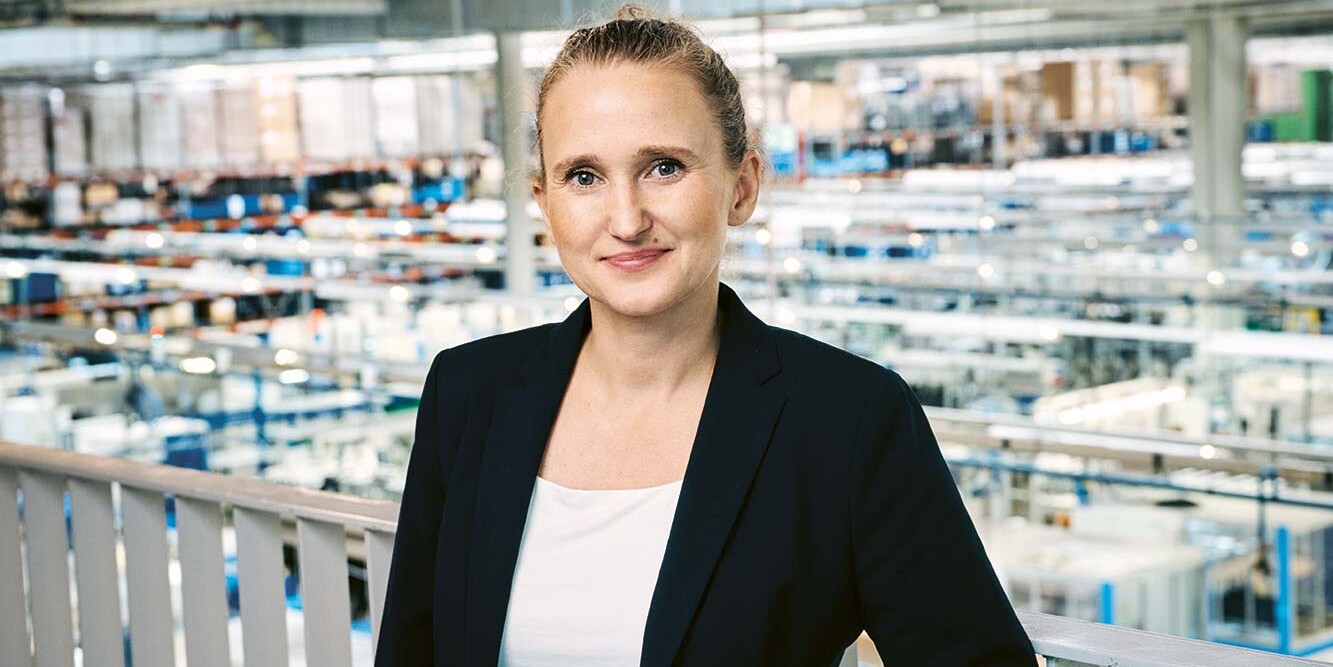
Agnieszka Zając has been managing the HOERBIGER plant in Bolesławiec since 2015, where 250 employees manufacture performance-determining products for various HOERBIGER divisions. Her focus is on close customer relationships and a culture in which everyone works toward a common goal.
Agnieszka, your heart is in the automotive industry. How did that come about?
Agnieszka Zając — I was born with a passion for technology. My father is a great technician who sparked my interest in the subject at a very early age. My friends had dolls, while I much preferred playing with calipers and screwdrivers. So, after my schooldays it was clear that I should start studying engineering at the Wrocław University of Technology. During an internship I was able to gain my first experience in the automotive industry. Although that was a very intense time, I knew right away that I wanted to work in this industry after graduation.
And what happened next?
AZ — After graduating, like many of my fellow students, I started work in the IT industry as a programmer before I was offered the opportunity to help set up a plant for a German automotive supplier in Legnica. I started as a quality engineer for the new plant, but very quickly I was able to take over the management of the quality department and thus the responsibility for all the company’s plants. Then, in 2012 I joined HOERBIGER as Quality Manager of the Bolesławiec plant, which I have been managing since 2015.
You produce not only for the Automotive Division, but also for other HOERBIGER Business Fields. What happens at your plant?
AZ — We manufacture a wide range of products. For the Automotive Division, we produce hydraulic and pneumatic parts for many well-known automotive manufacturers. For the Automotive Division, among others, we produce hydraulic and pneumatic parts for many well-known automotive manufacturers as well as blanks for sleeve production in Oberstenfeld and Schongau. And last but not least, we also work for the Engine Business Unit, for which we manufacture injectors.
Is such a broad product range an advantage or more of a challenge?
AZ — Both! For me as a plant manager, it’s a clear advantage if we have customers from different industries. This makes it easier to balance out fluctuations in orders. For my team, on the other hand, the large number of different products is a real challenge because it brings with it an incredible variety of processes. I can proudly say that my colleagues have expertise that’s extraordinarily broad and at the same time deep. Without such skills it would not be possible to produce so many different parts.
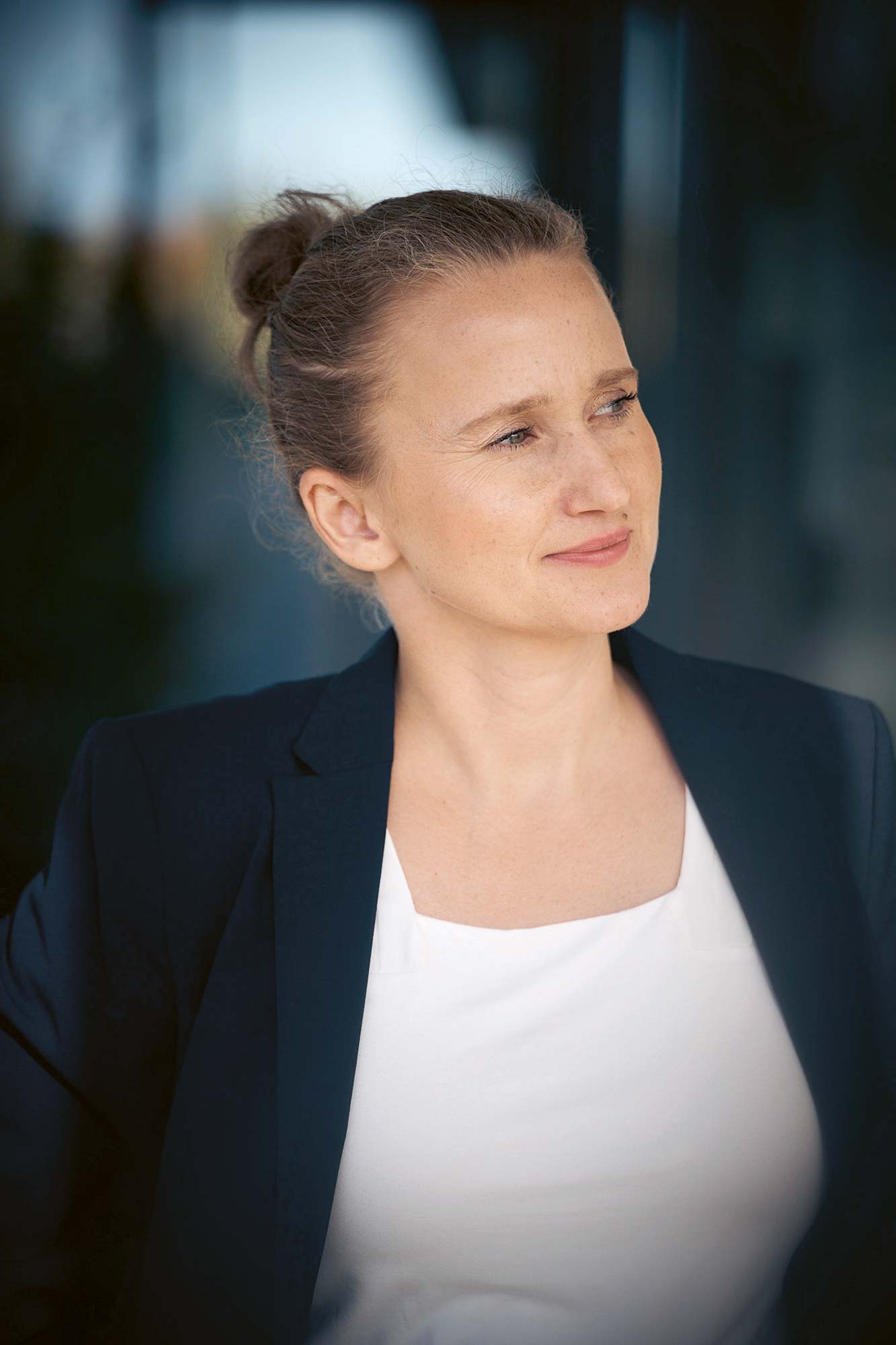
"I consider it a great privilege that I have been working with many of my colleagues for a very long time and that we can rely on each other one hundred percent."
Automotive Division
So does that make it difficult to find new colleagues for the team?
AZ — HOERBIGER is very well known in our area and enjoys an excellent reputation in the industry. That makes the situation here somewhat more relaxed than in other countries. But we work hard to be seen as an attractive employer. We offer very good working conditions, and we invest a lot of energy in training and further education. Particularly important to me personally are the good working atmosphere and the positive corporate culture that we cultivate together. In my opinion, these are one of the most important criteria, which is why we can keep up with the major local automakers.
Your team and you place great emphasis on innovation, whether it’s developing new products or optimizing processes. How do you personally deal with the need to constantly question or even reinvent yourself?
AZ — For an engineer, there’s nothing better than solving a tricky problem or tinkering around with something new, is there? No, seriously: I enjoy constantly questioning myself in order to optimize or rethink things. Anyone who works in production knows that what’s good today won’t be enough tomorrow. This is the only way we can achieve our goals of increasing the quality of our products, reducing manufacturing costs and protecting the environment through continuous improvement.
A particular strength of the plant in Bolesławiec is your close customer relationships. How does this cooperation work in practice and what are the advantages for our customers?
AZ — Being close to our customers enables us to respond to their requirements in a much more targeted way. The automotive industry is undergoing enormous change and the pressure is correspondingly great. Through our openness, speed and flexibility, we have earned the trust of our customers over the years. They know that they can rely on us and that we will stand by them as a partner in the development and series production of their future products.
What’s the most difficult task in your job as plant manager?
AZ — A plant is a very complex system. My most difficult and at the same time most important task is to create a culture in which all teams work toward a common goal. This is the only way to reconcile the individual goals of colleagues from production, quality and logistics. Even though we have detailed discussions every day, as a team we also have an overarching, common goal. I consider it a great privilege that I have been working with many of my colleagues for a very long time and that we can rely on each other one hundred percent.